我们构建了一个散射模型来描述基于这些观察的散射数据,如图 7a 所示。以原位实验 630 分钟采集的 USAXS 数据为例,该模型由两个部分组成。第一个分量是散射基线,它是在热处理前在室温下在相同的样品体积上获得的。第二个分量代表源自 δ 相沉淀物的过度散射。如前所述 [21],我们使用类似于具有两个散射级别的统一小角度散射方法的分析方法描述了这种过度散射 [48]。总之,这个双分量模型通过整个数据序列很好地描述了原位 SAXS 数据。
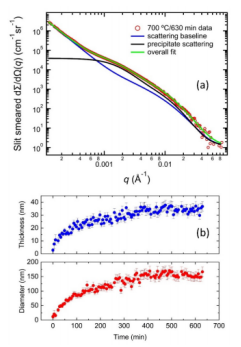
图 7. (a) 本工作中使用的 SAXS 模型的说明。 数据是在 700°C 的热处理过程中在 630 分钟时获得的。 超调散射包括两部分:(1) 散射基线和 (2) δ 相沉淀的过度散射。 (b) δ相沉淀物的平均直径(主要尺寸)和厚度(次要尺寸)随时间的演变。
图 7b 显示了 700°C 时δ 相沉淀物的平均厚度(小尺寸)和直径(大尺寸)随时间的演变。厚度和直径表现出类似的趋势,最初快速增加,然后逐渐增加。热处理结束时,平均厚度和直径分别为 34 ± 2 nm 和 154 ± 7 nm。这些值明显小于在 870°C 下 10 小时后从 AM IN625 获得的值,其中平均厚度和直径分别为 52 ± 5 nm 和 961 ± 94 nm [21],再次表明在700℃。在典型的残余应力热处理的背景下,在 870°C 下热处理一小时后,平均厚度和直径分别为 45 ± 4 nm 和 424 ± 40 nm [21];在 800 °C 下进行两小时热处理后,平均厚度和直径(取决于构建条件)分别介于 61 nm 至 77 nm 和 416 nm 至 634 nm 之间 [24]。换句话说,在 700°C 下进行长达 10 小时的应力消除热处理会导致 δ 相沉淀物明显小于 AM 625 典型残余应力热处理过程中产生的沉淀物。
值得注意的是,在 870°C 观察到的 δ 相析出物的连续粗化在 700°C 时并不明显,这表明在 700°C 下对显着粗化的稳定性,这可能是由于由弹性能提供的稳定性。被沉淀物包围的应变场 [49]。在 700 °C 的长时间热处理过程中,δ 相析出物的有限生长是很重要的,因为过度生长的 δ 相导致断裂应变降低 [50]。此外,最近的一项综述表明,在 700°C 下直接时效 24 小时也导致 AM IN625 的最高 UTS (1222 MPa) 和屈服强度 (1012 MPa),表明较小沉淀物的形成有助于提高机械性能。强度 [51]。
与先前报道的 800°C 和 870°C 动力学相比,我们观察到 AM IN625 中 700°C δ 相沉淀的析出速度明显更慢。为了使我们的观察合理化,我们使用热力学计算来了解沉淀动力学。
在我们的模拟中,我们假设所有的析出物都是球形的。我们还假设成核发生在位错上,因为预先存在的界面有助于降低成核的表面能垒[52]。在 AM 加工过程中,由局部极端加热和冷却条件引起的压缩拉伸残余应力循环导致局部位错密度的不均匀分布 [53]。与之前的工作 [33] 一致,我们假设位错密度为 ≈5 × 1011 m-2 。该位错密度对应于≈1021 m-3 的成核位点密度。对于析出模拟,我们考虑了 δ、γ 00、MC 碳化物、μ 和 σ 析出物,基体相为 γ。我们假设 γ/γ 00 、γ/δ、γ/MC、γ/μ、和 γ/σ 界面,分别。关于模拟的更多细节可以在别处找到[33]。
由于微观偏析,相邻枝晶间区域之间的成分不均匀。先前的 SEM 测量表明,制造的 AM IN625 的二次枝晶臂间距约为 300 nm [19]。 DICTRA 模拟表明,微偏析被限制在距枝晶间中心约 20 nm 的范围内 [33]。换句话说,平均成分代表重新分布的成分的良好近似。
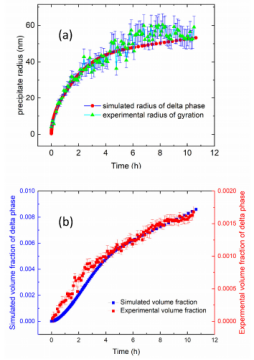
图 8. (a) δ 相沉淀物在 700 °C 下计算(模拟)半径和实验平均回转半径之间的比较,作为退火时间的函数。 在这里,我们为模拟的析出物假设了球形形态。 因此,我们根据图 7b 中报告的实验值计算了血小板 δ 相沉淀物的回转半径。 (b) δ 相在 700 °C 时的计算和实验体积分数作为时间的函数的比较。
图 8 显示了实验结果与标称成分的 TC-PRISMA 预测之间的比较。由于我们在模拟中假设沉淀物为球形,因此我们将观察到的片晶尺寸转换为回转半径 (Rg) 以进行直接比较,如下 Rg2 = R2/2 + D2/12,其中 R 和 D 代表直径和厚度分别如图 7b 所示。图 8a 显示模型预测的半径和有效测量的 Rg 遵循与模拟半径相似的动力学趋势 略小于实验值,如 Rg 所反映。当我们用调整到富集枝晶间区域的成分模拟沉淀反应时,我们的模拟预测具有相似动力学时间尺度的稍大的沉淀物。因此,预计与枝晶间区域和枝晶相关的模拟沉淀半径的加权平均值更接近实验值。图 8b 显示了模拟的时间相关体积分数和实验体积分数,按照之前详细的协议获得,具有类似的趋势,只是实验值小了约 5 倍。这种差异与先前报道的在 800°C 和 870°C 下获得的结果相似。有几个因素可能导致数量上的差异,包括析出物的假定球形几何形状、位错密度和界面能的温度依赖性。尽管有这些保留,考虑到模拟的近似性质,我们的结果仍然代表模拟和实验之间的良好一致性。
4。结论
在这项工作中,我们对使用 L-PBF 制造的 AM IN625 合金在 700°C 热处理过程中的析出动力学进行了详细分析。尽管之前报道的 800°C 和 870°C 残余应力热处理可以有效降低残余应力,但它们会导致形成大量体积分数的大 δ 相析出物,为需要良好延展性、断裂韧性、和耐腐蚀性。我们的非原位 SEM 数据表明,与 800°C 相比,700°C 的热处理导致 δ 相沉淀的析出显着更慢。原位同步加速器 XRD 数据表明,δ 相是 700 摄氏度时唯一可观察到的沉淀相。 FCC 基体和 δ 相的瞬态晶格参数表明 FCC 晶胞不断收缩,δ 相晶胞不断膨胀,这与 Nb 和 Mo 从基体相缓慢扩散到δ 相。原位 SAXS 结果表明,与 800°C 和 870°C 相比,δ 相沉淀物的形态演变在 700°C 下表现不同。片晶δ相沉淀物的主要尺寸在 700°C 下 10.5 小时后达到稳定值 154 ± 7 nm,这与在 870°C 下 10 小时后持续增加的主要尺寸达到 961 ± 94 nm 形成对比。在残余应力热处理的背景下,在 700°C 下进行长达 10 小时的应力消除热处理会导致 δ 相沉淀物(主要尺寸 ≈150 nm)显着小于 AM 的典型残余应力热处理过程中产生的沉淀物625(在 870°C 下一小时或在 800°C 下两小时后,主要尺寸≈500 nm)。我们还将实验结果与基于 TC-PRISMA 的降水模拟进行了比较。模拟捕获了沉淀动力学的总体趋势,观察到的和模拟的沉淀尺寸之间具有良好的一致性。模拟高估了析出物的体积分数,这可能是由于析出物的假定球形几何形状、位错密度的影响以及界面能的任何温度依赖性等因素造成的。总的来说,这项工作明确地确定了 AM IN625 在 700 ºC 下的 δ 相沉淀动力学比在 800 ºC 或 870 ºC 下显着慢,这是通常用于消除残余应力的温度,并且这项工作还提供了严格的微观结构探索 AM IN625 的低温应力消除热处理的可行性所需的动力学数据。