一、简介
Inconel®625 (IN625) 是一种镍基固溶体高温合金,具有通过 Nb/Mo 溶质强化的 Ni-Cr 基体 [1]。 IN625具有高强度、高断裂韧性和良好的耐腐蚀性能,在船舶和能源行业有很多应用,例如涡轮发动机部件、燃料和排气系统以及化学加工部件。 IN625还具有优良的焊接性和抗热裂性。这些特性使 IN625 成为各种增材制造 (AM) 技术[2-7] 的近期新进展中的主要合金,在当今使用的 5500 多种合金中,只有少数现有合金符合 AM 强加的严格的可印刷性标准 [8] ]。
可印刷性代表了 AM 的固有和基本挑战。与这一挑战相关的一个核心问题是在快速凝固和随后的热循环过程中产生的残余应力,局部冷却速率高达 1×106°C/s 到 1×107°C/s [9]。例如,AM IN625 上的中子衍射测量表明,在单个组件内,残余应力变化可高达 1 GPa [6,10]。这种量级的残余应力会导致零件变形,引入致命缺陷,并对制造零件的机械性能和性能产生不利影响 [11,12]。虽然已经开发了多种策略来减少制造过程中引入的残余应力,例如优化扫描模式 [13,14] 或加热基板 [15],但消除应力热处理仍然是较常见和比较可靠的方法以减轻残余应力。
与 AM 相关的另一个普遍现象是微隔离 [16,17]。在传统的制造过程中,宏观偏析表现为从毫米到厘米甚至米的长度尺度上的成分变化 [18]。 AM 中熔池的有限尺寸会产生更多局部微偏析,这主要是由于合金元素在液相和固相基体相中的溶解度不同。在镍基高温合金(如 IN625)中,微观偏析导致难熔元素(例如 Mo 和 Nb)在枝晶间区域附近的高浓度 [19]。分配系数 k,定义为枝晶中心和枝晶间区域的质量浓度比,描述元素偏析的程度。在 IN625 焊缝中,Mo 和 Nb 的 k 值通常分别为 0.95 和 0.50 [20]。在使用粉末激光床融合 (PLB-F) 制造的 AM IN625 中,热力学模拟预测 Mo 和 Nb 的 k 值分别约为 0.3 和 0.1 [19]。换句话说,与传统焊接工艺相比,增材制造可能导致更局部和更极端的元素偏析。
消除残余应力的需要和微偏析的存在会对微观结构控制和优化产生不利的影响。 AM IN625 就是一个很好的例子,因为它的局部成分远远超出 IN625 的标准成分范围,尽管粉末成分和平均标称成分都在标准范围内,但制造出来的零件并不是到处都是 IN625 [21]。按照 AM 机器制造商的建议,在 870°C 下进行一小时的应力消除热处理 [22],对于消除残余应力非常有效。然而,它也引入了大量的大 δ 相沉淀物,这是对 IN625 性能产生负面影响的相。在 800°C 下进行两个小时的替代应力消除热处理也证明对降低残余应力是有效的。然而,它仍然会产生大量 δ 相沉淀物,主要尺寸超过 600 nm。一个单独的策略是使用高温均质热处理完全消除微观偏析。例如,在 1150°C 下热处理一小时可使合金完全均质化。然而,这种热处理促进了晶粒生长,并且由于温度平衡所需的时间以及所需的高退火温度,对于工业规模的大型零件来说,实施起来既具有挑战性又成本高昂。
这些复杂的因素促使工业需要研究使用低温应力消除热处理的可行性。为了了解 AM IN625 的微观结构响应,在本研究中,我们主要使用基于同步加速器的原位散射和衍射方法研究了 AM IN625 合金在 700°C 下的固态转变动力学。具体来说,我们使用 X 射线衍射来监测相变动力学和小角度 X 射线散射来评估沉淀物的形态变化。与大多数关于热处理对镍基高温合金影响的研究相比,在实验中证据主要是从显微镜和内部 X 射线衍射数据中收集的,同步加速器测量通过原位实验探测固定且明显更大的样品体积,从而可以明确确定退火动力学。 这样的结果也更具统计代表性。 来自相同样品体积的动力学结果通过 CALPHAD(相图和热化学计算机耦合)方法的热力学预测来阐明。
2。材料和方法
2.1. 材料制作和样品制备
在 ASTM 增材制造镍合金 UNS N06625 标准规定的允许成分范围内。供应商提供的成分列于表 1 中。制造参数包括 Nd:YAG 激光器,工作功率为 195 W,扫描速度为 800 mm/s,舱口间距为 100 µm。在制造过程中,熔池宽度在 105 到 115 µm 之间变化。关于制造的更多细节可以在别处找到[19]。
表 1. 本工作中使用的原始 IN625 原料粉末的测量组成,由供应商提供的数据表提供,并根据 ASTM E1019 标准以及 IN625 的允许组成范围确定。质量分数在5%到25%之间的元素的测试相对不确定度为值的±5%,质量分数在0.05%和4.99%之间的元素为值的±10%,质量分数小于0.049%的元素是值的±25%。

2.2. 原位扫描电子显微镜(SEM)
我们使用扫描电子显微镜 (SEM) 对制造和热处理的样品进行异位显微结构检查。 JEOL S-7100F (JEOL, Ltd., Akishima, Tokyo, Japan) 场发射 SEM 配备了 Oxford X-MAXN (Oxford Instruments Plc., Abingdon, UK) 能量色散 X 射线光谱 (EDS) 检测器。我们在 15 kV 下操作 SEM。
为了评估热处理对 IN625 微观结构的影响,我们将 IN625 样品封装在真空安瓿中,并在 700°C 和 800°C 下进行热处理。我们按照标准金相程序抛光 SEM 样品,用王水蚀刻表面,并用 SEM 进行微观结构分析。对于这种表征,成像样品表面平行于构建方向,允许捕获树突和树突间区域的微观结构信息。
2.3.原位同步加速器小角度X射线散射和X射线衍射
我们在美国阿贡国家实验室高级光子源的 USAXS 设施中进行了基于同步加速器的原位超小角 X 射线散射 (USAXS)、小角 X 射线散射 (SAXS) 和 XRD 测量[23]。原位 USAXS 和 SAXS 监测由热处理引起的固态转变过程中的形态变化。在其检测范围内,原位 XRD 提供有关固态转变性质的信息。结合起来,USAXS、SAXS 和 XRD 覆盖了从 1 × 10-4 Å-1 到 ≈6.5 Å-1 的连续散射 q 范围。这里,q = 4π/λ sin(θ),其中 λ 是 X 射线波长,θ 是散射角 2θ 的二分之一。有关此设置的更多详细信息可以在其他地方找到 [24]。
在这项研究中,我们使用了 21 keV (λ = 0.5904 Å) 的单色 X 射线。样品处的 X 射线通量密度约为 1013 mm-2 s -1 。将制造好的样品机械抛光至约 50 µm 的厚度。我们使用 Linkam 1500 热台来控制温度。在室温下进行初始测量后,我们在 700°C 下进行了 10.5 小时的等温保持,从室温到目标温度的加热速率为每分钟 200°C。 USAXS、SAXS 和 XRD 的数据采集时间分别为 90 秒、30 秒和 60 秒,测量时间分辨率约为 5 分钟。测量体积区域的空间尺寸对于 USAXS 为 0.8 mm × 0.8 mm,对于 SAXS 和 XRD 为 0.8 mm × 0.2 mm。
2.4. 热力学计算
高温合金 [25,26]。为了与实验观察到的降水事件进行比较,我们使用 TC-PRISMA 模块 [27-29] 计算了降水动力学。该模块基于 Langer-Schwartz 理论 [30] 和 Kampmann-Wagner 数值方法 [31,32],通过整合 CALPHAD 提供的热力学和扩散信息,计算多组分和多相系统中析出物的成核、生长和粗化说明。模拟输出包括粒度分布、数密度、平均半径和体积分数的随时间演变。关于 CALPHAD 计算的更多细节可以在别处找到 [33]。
3。结果与讨论
图 1 显示了表 1 中列出的粉末成分的平衡 Nb 等值线。除了 FCC 基体之外,MC、M23C6、σ、P 和 δ 是热力学稳定的平衡相。 δ 尤其是在 600 至 ≈1200 ℃ 的宽温度范围内是稳定的,这取决于 Nb 的质量分数。我们之前已经确定,由于液相和固相中溶解度的差异导致溶质排斥,在预制的 IN625 中存在显着的枝晶间区域的微观偏析 [19,34]。 Scheil-Gulliver 模型和 DICTRA 预测的基于 CALPHAD 的凝固模拟使用有限元分析热模型预测作为输入表明 Mo 和合金元素的极端微观偏析铌。 例如,预测的 Nb 质量分数在二次枝晶核之间从 ≈2% 到 ≈22% 不等,这远远超出了 3.15% 到 4.15% 之间的 Nb 允许范围(表 1)。 先前的同步加速器 SAXS 测量表明,微偏析集中在枝晶间中心附近,尺度为 10 nm [35],这与模型预测一致 [19]。 这种极端的微观偏析有效地使制造的 IN625 零件在所有地方都不符合 IN625 的规格,从而导致该合金发生意外和有害的固态转变。
图 2 显示了 AM IN625 在四种不同条件下的 SEM 图像(图 2a,制造时,图 2b,700°C 下一小时,图 2c,700°C 下 24 小时,图 2d,800°C 下一小时C),成像表面平行于构建方向。在所有四个图像中都可以看到树枝状微观结构。对制造试样的 EDS 分析表明,枝晶间区域富含 Nb 和 Mo,枝晶区域富含 Ni 和 Cr。不同热处理条件对微观结构的影响是微妙的,在 700°C 下热处理一小时导致在测量条件下没有视觉上可观察到的差异。相比之下,在 700 °C 下长时间的热处理促进了在枝晶间区域附近形成片状形态的沉淀物。该相的形态与之前对 δ 相的观察一致,Nb 和 Mo 浓度越高,δ 相的成核越有利[33]。
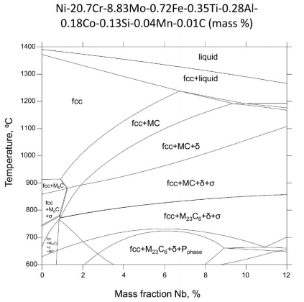
图 1. IN625 相图的稳态 Nb 等值线截面,假设成分为 Ni-20.7Cr-8.83Mo-0.72Fe-0.35Ti-0.28Al-0.18Co-0.13Si-0.04Mn-0.01C(质量百分比) )。
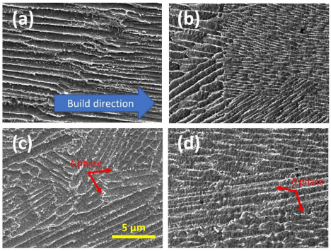
图 2. AM IN625 在四种不同条件下的微观结构 (a) 制造时,(b) 在 700 °C 下热处理一小时后,(c) 在 700 °C 下热处理 24 小时后,以及 (d) ) 在 800 °C 下热处理一小时后。 成像表面都平行于构建方向。 (c,d) 中的红色箭头突出显示了血小板 δ 相沉淀物。
如图 2c(700°C 下 24 小时)所示,在 800°C 下进行 1 小时热处理会导致类似的微观结构变化,并形成 δ 相沉淀物。我们注意到,在图 2c、d 中,δ 沉淀物的尺寸相当。热处理持续时间的差异表明 δ 相沉淀物的析出动力学在 800°C 时比在 700°C 时大大加速,这与之前为 AM IN625 构建的 TTT 图 [33,36] 一致。析出物生长的这种减缓对于残余应力消除热处理来说可能是显着的。先前的中子衍射残余应力实验表明,在 870°C [6] 下进行 1 小时热处理和在 800°C [10] 下进行 2 小时热处理可以有效地将残余应力降低到初始制造时的 13% 以下水平。然而,在这些温度下的热处理为δ相沉淀物的沉淀创造了有利的热力学条件。在这两种情况下(870°C 下一小时和 800°C 下两小时),δ 相沉淀物的主要尺寸具有 ≈500 nm 的可比标称尺寸 [21,24]。这些大的析出物优先在枝晶间区域生长,降低了 IN625 的延展性、断裂韧性和耐腐蚀性 [37,38]。
图 3 显示了 AM IN625 的原位 XRD 数据,该数据在 700°C 等温保持 10.5 小时期间获得。 在室温下热处理之前获得的 XRD 数据表明,IN625 在其制造状态下具有 FCC 基质相,晶格常数为 (3.595 ± 0.002) Å,没有额外的可检测相。 值得注意的是,同步加速器 XRD 测量是使用单光子计数探测器通过高通量和高穿透性 X 射线进行的。 这种测量灵敏度意味着相图中预测的平衡相而不是基体相没有足够的时间在构建过程中形成任何显着数量。 单相制造的基质相代表了后续固态相变的起点。
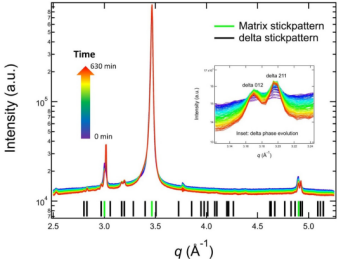
图 3. AM IN625 在 700°C 等温热处理期间获得的原位同步加速器 XRD 数据。 插图显示了 δ 012 峰和 δ 211 峰的演变。 数据采集时间遵循箭头色标。 计算出的棒状图案对应于 FCC 基质相和正交 δ 相。
在热处理过程中获得的原位 XRD 数据使我们能够监测热致相变。如图 3 所示,XRD 数据在 700°C 下持续演变,主要特征是新峰族的峰强度单调增加。这些新峰属于正交结构。图 3 中的棒状图案是基于晶格参数分别为 5.109 Å、4.232 Å 和 4.487Å 的正交相和晶格常数为 3.626 Å 的 FCC 相计算得出的。这些晶格参数是 700°C 时的值,用于直接比较棒状图案和原位实验数据。 δ 峰较弱。因此,我们使用插图来突出 δ 相的两个特征峰(δ 012 和 δ 211)的时间相关变化。除了峰强度的持续增长之外,我们还观察到峰宽变窄,这表明沉淀物增长。
基于原位 XRD 的仔细分析可以揭示 FCC 基质和沉淀物的结构变化。图 4 显示了 FCC 矩阵的晶格常数的演变。我们观察到晶格常数单调下降,表明原子半径大的元素,如 Nb 和 Mo,逐渐从基体中耗尽。这种现象与消耗 Nb 和 Mo 的 δ 相沉淀物的沉淀一致,如图 3 所示。在暴露于服务的 IN625 中也观察到了与 δ 相沉淀物沉淀相关的基体晶格参数的降低 [39] ,除了需要在 850°C 下进行长时间的热处理(500 小时)才能检测到晶格参数的变化。
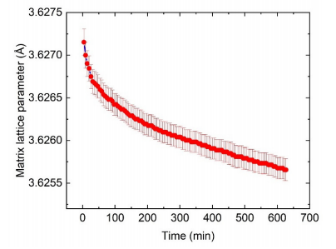
图 4. 基体晶格常数的时间依赖性,从 700°C 下的原位 XRD 测量中获得。 我们观察到晶格参数单调下降,表明重元素如 Nb 和 Mo 从固溶体基质中逐渐扩散,并有助于 δ 相的成核和生长。 除非另有说明,本图中和下文中报告的不确定度代表一个标准偏差。
此外,固溶合金的基体晶格参数的变化与沉淀的程度有关 [40]。在 AM IN625 中,在 870°C 下热处理 10 小时之前和之后矩阵晶格参数的差异约为 0.0042 Å [21]。相比之下,在 700°C 下热处理 10.5 小时后,晶格参数变化 ≈0.0015 Å,表明在该温度下 δ 相的析出显着减少。
按照设计,IN625 是一种单相合金,其强度主要来自 Mo、Nb 和 Cr 的固溶强化 [1]。虽然预计基体中 Mo 和 Nb 的消耗会降低强度,但析出物的形成可以补偿这种降低并提高 IN625 的整体强度。例如,锻造的 IN625 在 700°C 下热处理 170 小时后达到其峰值硬度,这主要是由于 γ”相的析出,这是 δ 相的前体 [41]。同样,δ相的析出也会增加整体强度并降低延展性[37]。对于 AM IN625,需要并需要在一定温度范围内对热处理对机械性能的影响进行系统评估。
在热处理过程中,δ相的晶胞也发生变化。图 5 说明了这种变化。在三个正交晶格参数(图 5a-c)中,两个几乎恒定,分别为 ≈5.108 Å 和 ≈4.232 Å。第三个晶格参数显示从≈4.482 到≈4.488 Å 单调增加。已知δ相的长轴与FCC基体的密堆积方向一致,FCC基体与δ相的结晶取向遵循{111}FCC//(100)δ和FCC// [100]δ[10]。基于此,我们推断 Nb 和 Mo 的扩散也是有方向的。由于 Mo 从基体到 δ 相的扩散比 Nb 发生得更慢 [42],这种定向扩散可能导致 δ 相化学的变化和晶胞体积的增加,如图 5d 所示。
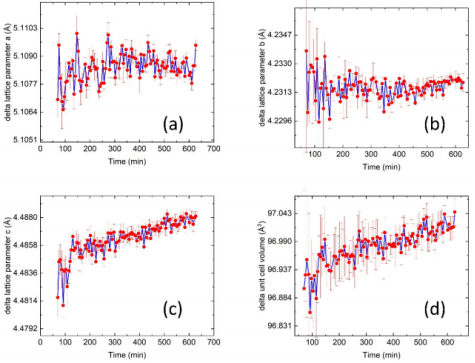
图 5. (a-c) δ 相沉淀物的三个晶格参数的时间依赖性,从 700°C 下的原位 XRD 测量获得。 (d) δ 相析出晶胞的体积。
在等温热处理期间使用相同样品体积获得的原位 SAXS 数据也提供了一个窗口来探测材料微观结构的统计显着转变动力学。图 6 显示了完整的数据集,USAXS 数据是主图,SAXS 数据显示在插图中。为保持一致性,散射数据使用与图 3 中的 XRD 数据相同的色标进行颜色编码。散射数据具有三个显着特征。首先,对于散射数据的非常低 q 部分(≈1 × 10−4 Å−1 到 ≈4 × 10−4 Å−1 ),我们观察到幂律斜率不随时间。我们将此特征归因于颗粒散射,这类似于之前对镍基高温合金 [21,43] 和铝合金 [44,45] 的研究。 IN625 中的晶粒生长对于低于 900°C 的温度是最小的 [46]。因此,预计颗粒散射是稳定的,这与实验观察一致。其次,我们观察到散射强度在 ≈4 × 10−4 Å−1 和 ≈0.01 Å−1 之间单调增加,特别是在 2 × 10−3 Å−1 和 8 × 10−3 Å−1 附近有两个吉尼尔区域, 分别。由于原位 XRD 数据和非原位 SEM 图像仅显示 δ 相沉淀物,我们将此散射信号归因于 δ 相。先前的显微研究已经确定δ相沉淀物是具有两种特征尺寸的片晶[10,21,47],这与散射数据中两个吉尼尔区域的观察结果一致。最后,插图中显示的 SAXS 数据是 USAXS 数据中高 q 幂律斜率的简单扩展;即,SAXS 数据不包含额外信息,这表明在此热处理过程中没有形成额外的纳米级沉淀物。
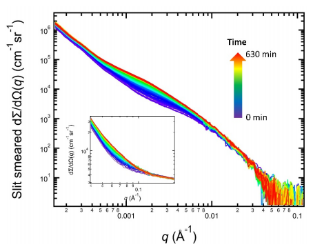
图 6. AM IN625 在 700°C 等温热处理 10.5 小时期间获得的原位 SAXS 数据。 主图和插图分别显示了 USAXS 和 SAXS 数据。 采集时间按照时间箭头进行颜色编码。 USAXS 强度是狭缝涂抹的。